金属研磨とは|素材・仕上げ別の最適手法と品質向上
投稿日: 2025-07-14
素材の特性を活かした最適研磨を成功に導くヒント集
金属研磨は、製品の美観向上からバリ除去、摩擦低減、錆取りまで多彩な目的を持つ仕上げ工程です。
本記事では、光沢発生の原理から「鏡面」「サテン」「マット」「ブラッシュ」といった代表的な仕上げの特徴・用途・研磨方法、素材別の前加工、主要な研磨技術、トラブル対策やFAQなど、現場で役立つ知見を幅広く解説します。
金属研磨の目的と必要性
金属研磨が必要とされるケース
本節では、具体的にどのような場面で金属研磨が必要とされるのか、目的別に整理して解説します。
- 美観向上(装飾・ブランド価値)
- 研磨による表面仕上げは、製品の第一印象を左右する重要な要素です。たとえば、高級家電のフロントパネルに鏡面研磨を施すと光を反射して高級感が増します。
建築用ドアハンドルや手すりのサテン仕上げでは、傷が目立ちにくく落ち着いた質感が空間に調和します。
また、自動車エンブレムやジュエリーケースには鏡面研磨が多用され、ブランド価値を際立たせる演出効果を発揮します。
適切な金属研磨を選ぶことで、装飾性と高級感が高まり、製品の魅力と競争力を大きく向上させます。
バリ除去
- 砥石切削やプレス抜き加工では細なバリが発生することがあります。
バリが残ると、部品同士が擦れてキズが入るほか、摩耗が早まり、電気回路でショートを起こす原因になります。
また、組み立て時に部品同士が正しくかみ合わず、寸法ずれが生じるなど、多方面で不具合を招きます。
摩擦低減による摺動性・耐久性向上
- 金属表面の凹凸が擦れ合うと抵抗と熱が生じるため、仕上げ研磨で鏡面や細かな筋目仕上げ(サテン仕上げ)を施し、表面粗さを低減して摩擦を抑えます。
潤滑油を併用すればさらに摩擦力が落ち、発熱や摩耗を防ぎます。
ただし油膜を安定させるには、微細な凹凸を残した「適度な粗さ」も重要です。金属研磨と潤滑の最適化で、軽快な動作と優れた耐久性を両立できます。
刃物の切れ味向上
- 刃先を研磨することで、先端に残った微細なバリを除去し、刃先に適度な丸みを持たせます。
これにより、切断時の刃先への衝撃を分散させ、欠けや摩耗を防ぎ、長期間にわたり安定した切れ味を維持できます。
金属めっき/塗装下地の「荒らし加工」
- 荒らし加工とは、めっきや塗装を行う前に金属表面にわざと凹凸をつける処理です。
ショットブラストやサンドブラスト、ベルト研磨などで微細な凹凸を作り、塗料やめっき層が均一に食い込むようにします。
これにより、仕上がりの密着性が向上し、剥がれや浮きを防止します。
特に高負荷や屋外暴露が想定される部品では、耐久性を確保するために欠かせない金属研磨の前処理工程です。
錆取り(防錆前処理)
- 既存の錆はワイヤーブラシや防錆剤で除去した後、金属研磨で平滑化します。
仕上げ研磨後は、防錆油を塗布して薄い油膜を形成したり、錆止め塗料で塗装するほか、高精度金型には真空包装で空気を遮断し長期防錆を行います。
これにより研磨で露出した素地を保護し、長期的に腐食を防止します。
💡ポイント
金属研磨は目的ごとに役割が異なり、美観・機能・加工精度を高めるために最適な方法を選ぶことが重要です。
金属光沢の原理
金属研磨が果たす役割の中でも、外観品質に直結する「金属光沢」は重要な要素です。
本節では、その光沢がどのような物理的仕組みで生まれるのか、また表面の粗さが見た目にどう影響するかを解説します。
金属光沢が生まれる物理的なしくみ
金属光沢は、金属内部の自由電子が光(電磁波)の電場に駆動されて集団的に振動(プラズマ振動)することで生まれます。
この振動が光を跳ね返し、金属内部への侵入を防ぐため、鏡のような反射光が得られます。
金属ごとの電子応答特性(プラズマ周波数や誘電率の違い)により、反射効率の波長依存性が生じ、異なる色調の光沢として見えます。
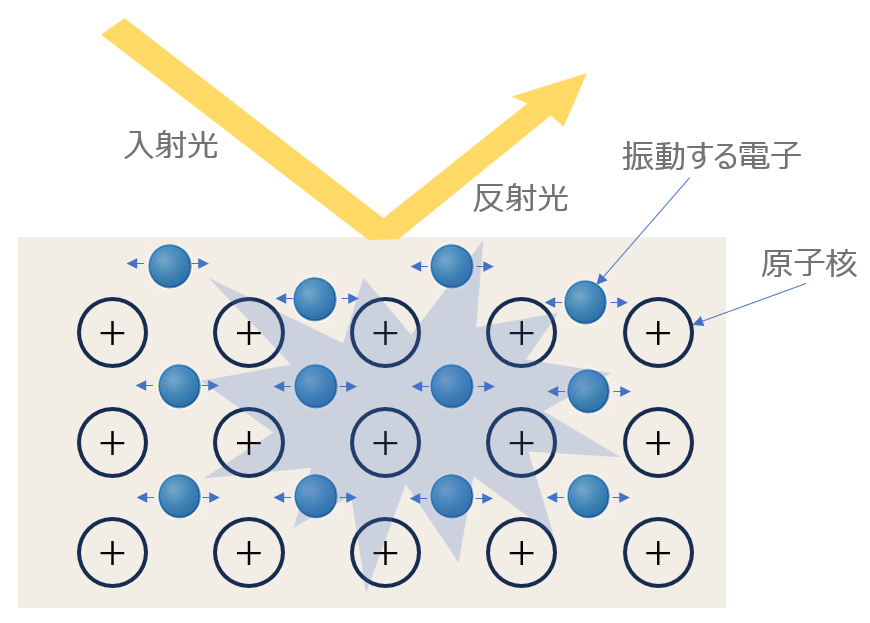
金属光沢の仕組み:自由電子による光の反射
表面粗さと反射の関係
- 鏡面(粗さ<<光の波長)
- 表面粗さが可視光(波長:約400~700nm)より十分に小さい場合、入射光は乱反射せず、入射角と同じ方向に反射されます(鏡面反射)。
鏡のように周囲を映し込む強い光沢が得られ、高級感や意匠性を演出します。
主な用途としては、反射ミラー、ポリッシュ加工されたステンレス面、装飾パネルなどがあり、美観を重視する製品に広く用いられます。
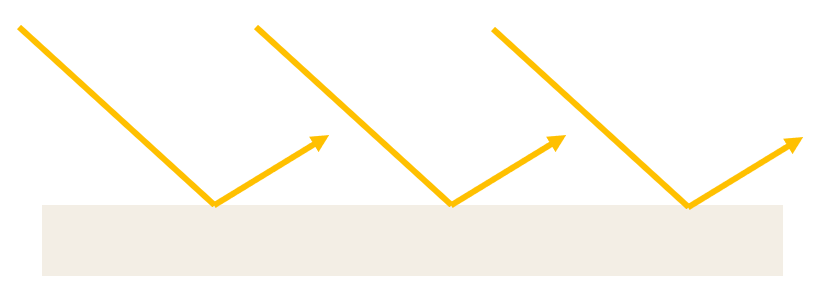
鏡面反射
- マット・拡散面(粗さ>>光の波長)
- 表面粗さが光の波長よりも大きい場合、多方向への乱反射が生じ、入射角に関係なく均一な拡散光となります。
これにより「ツヤ消し」や「落ち着いた質感」が得られ、機能性や安全性を求められる製品に適しています。
主な用途は、ショットブラスト面やサンドブラスト面などで、工業用外装や制御盤カバーなどに使用されます。
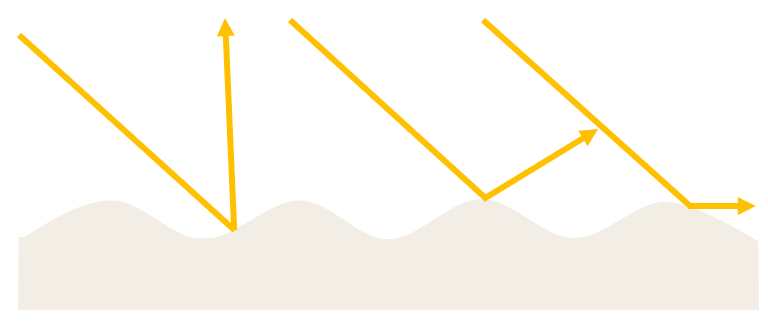
乱反射(マット)
💡ポイント 金属光沢は、自由電子が光を反射することで生まれます。
表面がなめらかだと鏡のような強い光沢に、粗いと落ち着いたマット調になります。
金属研磨で得られる仕上げの種類
金属研磨には、大きく分けて「鏡面」「サテン(ヘアライン)」「マット」「ブラッシュ(筋目)」の4つの仕上げがあり、それぞれ用途や雰囲気、最適な研磨方式が異なります。
以下では写真と合わせて、特徴・代表的な用途・おすすめの研磨方法を解説します。
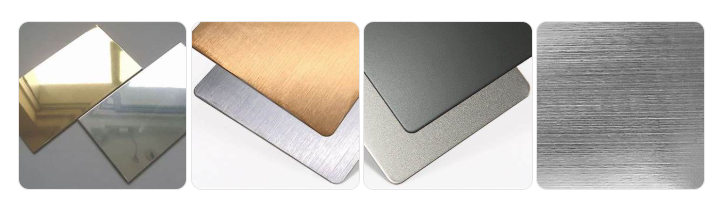
金属研磨による4種の仕上げの比較(鏡面・サテン・マット・ブラッシュ)
- 鏡面
- 特徴: 高い反射率を持つツヤツヤの仕上げ。まるで鏡のように周囲が映り込むほどの滑らかさと光沢感があります。
主な用途: 高級家電のフロントパネル、光学部品や反射ミラー、自動車エンブレム、宝飾ケースなど、高級感を演出する意匠性を求められる場面。
研磨方法: 布バフに微細研磨剤を組み合わせたバフ研磨、または鏡面研磨機SMAPによる安定した品質の研磨で実現されます。
サテン
- 特徴: 光沢は抑えつつも、繊細な筋目が走る落ち着いたツヤを出します。傷が目立ちにくく、方向性を持たせることで意匠性を演出します。
主な用途: 家電の外装パネル、厨房設備、建築パネル(エントランスドア)など。
研磨方法: ベルト研磨機を使用し、サンドペーパーや不織布ベルトで一定方向に研磨することで均一な筋目を刻みます。
- マット
- 特徴: 光の乱反射を活かした“つや消し”仕上げ。反射を抑えつつ、落ち着いた質感と均一な拡散光を演出します。
主な用途: 工業用外装部品(機械筐体、装置カバー)、光の反射を嫌う制御盤パネルや医療機器カバーなど。
研磨方法: ショットブラストやサンドブラストによる拡散加工、あるいはベルトサンダーで粗めの砥粒を用いたマット研磨を行います。
- ブラッシュ
- 特徴: 線状の筋目を強調した“ヘアライン”の一種で、やや粗いざらつき感を残しつつデザイン性を重視した仕上げです。高級感とともに、使い込んだ質感やヴィンテージ感を演出できます。
主な用途: 建築内装材(手すり)、インテリア金属(装飾パネル)など、空間デザインにアクセントを加える場面。
研磨方法: ベルト研磨で一定方向の筋を付けた後、ディスク研磨で筋目を整える2段階研磨を行います。
💡ポイント 金属研磨の仕上げには「鏡面」「サテン」「マット」「ブラッシュ」があり、見た目や用途に応じて最適な加工法が選ばれます。
それぞれ質感や光の反射の違いで印象が大きく変わります。
研磨が必要な金属とその特徴
金属研磨に先立つ前加工は、素材ごとに工程や加工性が大きく異なります。
以下では、代表的な金属ごとに、主な前加工方法や金属研磨における一般的な特徴をまとめます。
- スチール材
- スチール材は加工性に優れ、まずワイヤー放電加工(W-EDM)でおおまかな形状を切り出し、その後旋盤やフライス盤などで寸法を詰めます。
金属研磨工程では、切削時に生じる切削痕やバリを取り除くため、必要に応じて粗研磨→中研磨→仕上げ研磨の順に番手を細かく段階付けて行います。
特に高速切削による摩擦熱で表面が「焼け」やすいため、各研磨工程で十分な冷却を行い、色ムラや変質を防ぎます。
- ステンレス
- ステンレスは加工硬化を起こしやすく熱伝導率が低いため研磨中に摩擦熱が内部にこもりやすい金属ですが、耐食性が高いため各種研磨方法と相性がよいです。
W-EDMやプレス加工の後、金属研磨では「焼け」や色ムラを防ぐため切削熱を抑えることが必要です。
冷却液の適切な供給、研磨材の選定、研磨速度の調整を組み合わせることで、滑らかで高品質な研磨仕上げが可能になります。
- アルミ合金
- アルミ合金は柔らかく変形しやすく熱にも弱いため、プレス成形や板金曲げ、射出成形後にはバリや歪みが生じやすく、さらにバフ研磨など熱がかかると表面が焼けたり小さな凹凸が発生して研磨難易度は高いです。
成形直後の初期研磨でバリを除去し、その後は適切な圧力・研磨材・速度を組み合わせた研磨工程で表面を均一に仕上げます。
過度な圧力や高速研磨を避けることで、加工歪みや熱膨張による変形を最小限にします。
- チタン合金
- チタン合金は軽量かつ高強度でありながら、硬く粘り強い素材です。熱伝導率が極めて低いため、加工中に生じた摩擦熱が内部に蓄積しやすく、加工硬化を起こしやすいという特性があります。
通常はまずW-EDMで荒取りを行い、続いてフライス加工やラッピング研磨によって寸法精度と面粗さを仕上げます。
研磨工程では冷却を行いながら番手を段階的に細かくすることで、焼けや変形を防ぎつつ平滑な仕上げを実現します。
また、研磨材には炭化ケイ素やアルミナよりもダイヤモンド砥粒を用いるのが最適で、高品質な研磨結果を効率的に得ることができます。
- 銅・真鍮
- 銅や真鍮は柔らかく加工性に優れ、金属の中でも最も磨きやすい材質です。鋳造や切削で大まかな形状を作った後、プレスや鍛造で最終的な寸法に整えます。
研磨後はすみやかに洗浄を行い、防錆膜の塗布や真空包装で露出面を保護することで、酸化や変色を防ぎ、研磨後の美しい光沢を長期にわたり維持します。
また、銅・真鍮は型彫り放電加工の電極素材にも用いられ、この電極を丁寧に磨くことで被削材の表面粗さを大幅に改善する効果も発揮します。
- 超硬合金
- 超硬合金とは、タングステンカーバイド(WC)という非常に硬いセラミック粒子を金属のコバルトでつなぎ合わせた素材で、身近にはドリルやエンドミルといった切削工具として使われています。
加工時にはまずダイス切削やW-EDMで大まかな形を作りますが、この段階では刃先に「微小バリ」と呼ばれるごく小さな突起が残りやすく、そこから初期欠けといって刃先の端が欠け始めると、一気に切れ味が悪くなってしまいます。
そこで「ホーニング」と呼ばれる仕上げ工程を行い、専用の砥石やビーズで軽くこするようにバリを取り除くことで、刃先を滑らかに整えて欠けの発生を防ぎ、工具寿命を大幅に伸ばします。
その後のラッピング研磨では、ダイヤモンド砥粒を使って番手(粒度)を段階的に細かくしつつ冷却を行い、表面の微細な凹凸をきれいに均一化することで、超硬合金の高い耐久性を保ちながら深みのある光沢仕上げを実現します。
💡ポイント 金属ごとに硬さや熱の伝わり方が異なるため、最適な研磨方法も変わります。焼けや変形を防ぐには、冷却や番手調整など素材に合った工夫が重要です。
金属研磨の主な加工方法
ここでは金属研磨の主な加工方法の概要を解説します。
各加工方法の詳細な手順や装置については記事「研磨加工の基本と様々な研磨方法」をご参照ください。
この表は、主な金属素材(スチール、ステンレス、アルミ、チタン、銅・真鍮、超硬合金)に対する各研磨方法の適用度をマトリクス形式で示したものです。
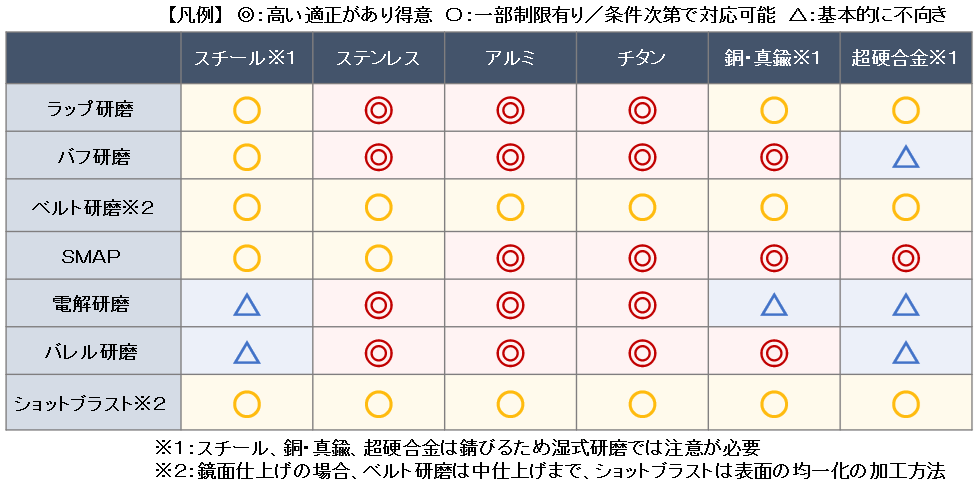
以下に、主要な金属研磨方法の概要を簡潔に解説します。
- ラップ研磨
- 加工原理: ダイヤモンドやアルミナなどの砥粒を用いて、平面同士を機械的に擦り合わせる。
主な用途/仕上がり: 粗研磨から鏡面仕上げまで対応。金型やレンズなど、高精度な平面加工に使用。
作業性・特徴: 機械による安定した加工が可能で、一定の作業効率が見込まれる。
- バフ研磨
- 加工原理: 布製バフにクロム酸化物などの研磨剤を塗布して表面を磨く。
主な用途/仕上がり: 光沢仕上げや意匠面の最終仕上げとして使用。
作業性・特徴: 基本は手作業だが、自動化装置との組み合わせにも対応可能。
- ベルト研磨
- 加工原理: 回転する研磨ベルトで素材表面を削る機械研磨方式。
主な用途/仕上がり: 筋目(サテン・ブラッシュド)など、方向性のある意匠仕上げに適する。
作業性・特徴: 均一な研削が可能で、外観の統一感を持たせやすい。
- 鏡面ショットマシン(SMAP研磨)
- 加工原理: 専用メディアを用いた独自の研磨技術。
主な用途/仕上がり: 平面・曲面を問わず、焼けや変形を抑えながら高精度な鏡面仕上げを実現。チタンや超硬合金などの難削材にも対応。
作業性・特徴: 熟練作業に頼らず、安定した品質管理が可能。
- 電解研磨・化学研磨
- 加工原理: 薬液と電流を用いて金属表面を化学的に溶解・平滑化する。
主な用途/仕上がり: 微細な凹凸や酸化皮膜を除去し、均一な平滑面を形成。配管内部や複雑形状など、機械研磨が難しい部品に適する。
作業性・特徴: 工具接触がなく、ワーク形状を変形させずに処理可能。
- バレル研磨
- 加工原理: 回転または振動するバレル容器内で、ワークと研磨材を相互に擦り合わせる。
主な用途/仕上がり: バリ取り、角取りに加え、方向性のない均質なマット仕上げが可能。ネジやプレス品などの金属小物に広く対応。
作業性・特徴: 大量処理が可能で、量産向けに適した自動処理が行える。
- ショットブラスト
- 加工原理: 圧縮空気で金属または非金属の微粒子を高速噴射し、表面を物理的に叩いて処理。
主な用途/仕上がり: 酸化被膜や汚れの除去、塗装・接着の下地処理、粗めのマット仕上げ。鋳造品や板金などの表面処理に利用。
作業性・特徴: 広範囲を短時間で処理可能。微細な凹凸により、機能性や外観特性の向上が期待できる。
💡ポイント 金属研磨には目的や素材に応じた多彩な加工法があり、光沢・質感・精度を左右する重要な選択ポイントとなります。
金属研磨関連でよくあるトラブルと防止策
金属研磨関連でよくあるトラブルとその原因、防止策を具体的に解説します。
- 研削焼け・変色
- 粗研削時の摩擦熱で表面が酸化し、青紫や茶褐色の焼けが発生します。切込み量・送り速度を抑え、砥石やベルトの切れ味を維持しつつ、冷却液や研磨液でしっかり冷却します。
もし焼けが残ったら、仕上げ研磨で表層を薄く削り落とします。
- バリ残り
- 切削・プレス加工後に微細なバリが取りきれず、組立不良や摩耗を招きます。
中間研磨を追加して番手を段階的に細かくするほか、専用のバリ取り工具や振動バレルを併用。
エッジ部はスポット研磨で仕上げます。
- 錆び発生
- 研磨後の素地が空気に触れて放置されると錆びが発生します。
防錆油や保護膜塗料を塗布し、金型などは真空パック+乾燥剤封入で長期保管します。
発生した錆は化学洗浄やワイヤーブラシで除去し、再度研磨後に防錆処理を行います。
- 研磨ムラ
- 治具の固定不良や研磨圧力・速度のバラつきで面に明暗ムラが出ます。
ワークを治具で均一に押さえ、研磨材を消耗度により定期的に交換します。
最終段階でラッピング研磨やバフ掛けを行い、均一な仕上がりに整えます。
- キズ・擦り傷
- 異物混入や研磨材の不純物、工具の接触ミスなどで微細キズが生じます。
研磨前にワークと研磨材を清掃し、異物排除を徹底。
研磨圧力は適正範囲内に管理し、傷が付いた場合は細番手の研磨材で部分的に磨き消し、最後にポリッシュでならします。
💡ポイント 金属研磨で発生する焼けやバリ、キズなどの不具合は、適切な工程管理によって防止し、仕上がり品質を安定させることができます。
FAQ | 金属研磨に関するよくある質問
金属研磨に関する知識は幅広く、用途や素材によって注意点も異なります。
ここでは、実用的な視点でわかりやすくお答えします。
- 鏡面研磨とサテンやマット仕上げはどう使い分ければよいですか?
- 鏡面研磨は高級感や反射性を重視する場面に最適です。
一方、サテンやマット仕上げは傷が目立ちにくく、落ち着いた印象を与えたい場合に適しています。
- 研磨後の錆を防ぐにはどうすればいいですか?
- 研磨後すぐに防錆油を塗布するか、表面処理(塗装やメッキ)を施すことが基本です。
長期保管の場合は、真空包装や乾燥剤との併用で空気や湿気を遮断しましょう。
- アルミや銅のような柔らかい金属は研磨で変形しませんか?
- 通常のバフ研磨やベルト研磨では、柔らかい金属に過度な圧力や熱が加わることで、歪みや変形のリスクがあります。
一方、SMAP研磨のようにワークに均一に力をかける専用装置を使う方法であれば、変形リスクを大きく抑えることができます。
研磨圧や熱の発生が最小限に制御されるため、アルミや銅といった変形しやすい素材でも安定した高品質な仕上げが可能です。
- 金属研磨の工程で注意すべき安全対策は?
- 一般的なバフ研磨やベルト研磨では、粉塵の飛散・火花・ワークの高温化といったリスクがあるため、保護メガネやマスク、手袋の着用は必須です。
また、換気や防火対策も重要です。
ただし、SMAP研磨のように粉塵や火花が発生しにくく、作業者への負荷が小さい研磨方式であれば、これらのリスクは大幅に軽減されます。
それでも基本的な保護具の着用は推奨されますが、従来工程と比較して安全性に優れるのが特徴です。
研磨加工に関するお悩みは東洋研磨材工業にご相談下さい
東洋研磨材工業は研磨機・研磨材の総合商社です。本社1階にテクニカルセンターを備え、最適な研磨方法のご提案、材質・用途に合わせた研磨材の選定、更には鏡面研磨機SMAPを始めとした研磨機の販売などを行っています。
研磨加工に関するお悩みは是非一度、東洋研磨材工業にご相談下さい。
お問い合わせ